Country
Chile
Application
Cooling Water
Water source
Seawater
Filtration solution
2 x 12 x 4" Galaxy batteries (100 micron)
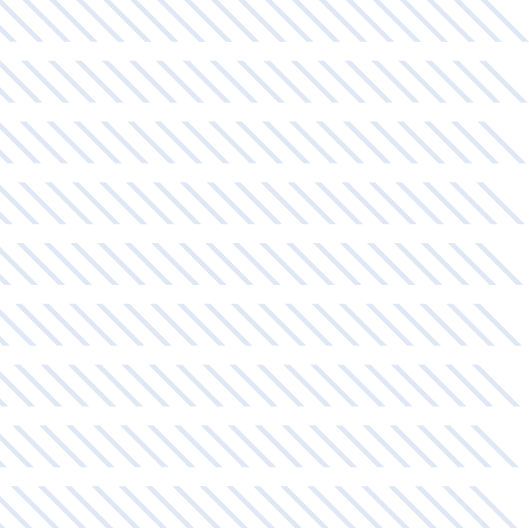
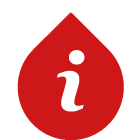
Background
AES Gener is the second generating company in Chile and the main thermoelectric generator, and provides 4.068 MW (including Guacolda S.A.), equivalent to a share of 22%, whereas 3.797 MW of thermoelectric capacity and 271 MW of hydroelectric capacity. The plant provides electrical power to the Norte Grande Interconnected System (SING) through its subsidiaries: Norgener S.A. (Norgener), Empresa Electrica Angamos S.A. (Electrica Angamos) and TermoAndes S.A. (TermoAndes) in Argentina. The Norgener complex has a coal thermal power station in the city of Tocopilla, northern Chile, which contributes with 277MW to the SING. At this location the turbine cooling system uses seawater. Cooling circuits usually contain deposited impurities associated with the origin of the water, which bring negative consequences including efficiency reduction in the heat exchange process and the need of continuous maintenance to remove these solids, finally resulting in loss of productivity.
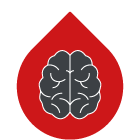
Challenge
The cooling circuit had fully manual metal screen filters, however, these did not deliver the proper water quality to protect the circuit and there was a high quantity of solids. The filters had a high degree of corrosion as the construction materials were not suitable for use with seawater. In addition, since the filters were manually operated, cleaning relied 100% on the operators. This required too much maintenance and manpower to clean the screen filter. The cleaning frequency was more than once a week, at difficult times of the day and night and there were even leakages to the outside because the filter casings were heavily corroded. This caused system delays and problems supplying good quality water for the cooling circuit. The customer decided that the best solution would be to have an automatic, self-cleaning filtration system, constructed of materials suitable for use with seawater with the goal of ensuring system continuity.
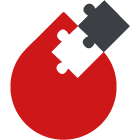
Solution
Amiad’s advantages compared to the competitors were its commitment with the client, the filter construction material and the system configuration as the space available for installation was restricted. Considering the available space, the solution designed for the required 1,400 m3/h flow rate was 2 units of 12 x 4″ SW Galaxy batteries (100 micron each) to be placed one on top of the other. This doubled to two refrigeration units. The washing process is performed with an external water source at 6 bar, with a customer-owned pump, head by head, i.e. 24 washes per system are performed.
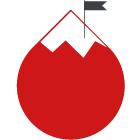
Results
The client is very satisfied with the results obtained by the filters; they have been operating since December 2016 and have been running as expected without any interruptions. Amiad’s filters have significantly improved the filtration quality, reducing the need to clean the heat exchanger after the filter and helped to decrease booster pump failure, also after the filter. Amiad supplied an automatic filtration system that is low in energy consumption, high in efficiency and performance that delivered the expected results.